More Details
Features & Benefits
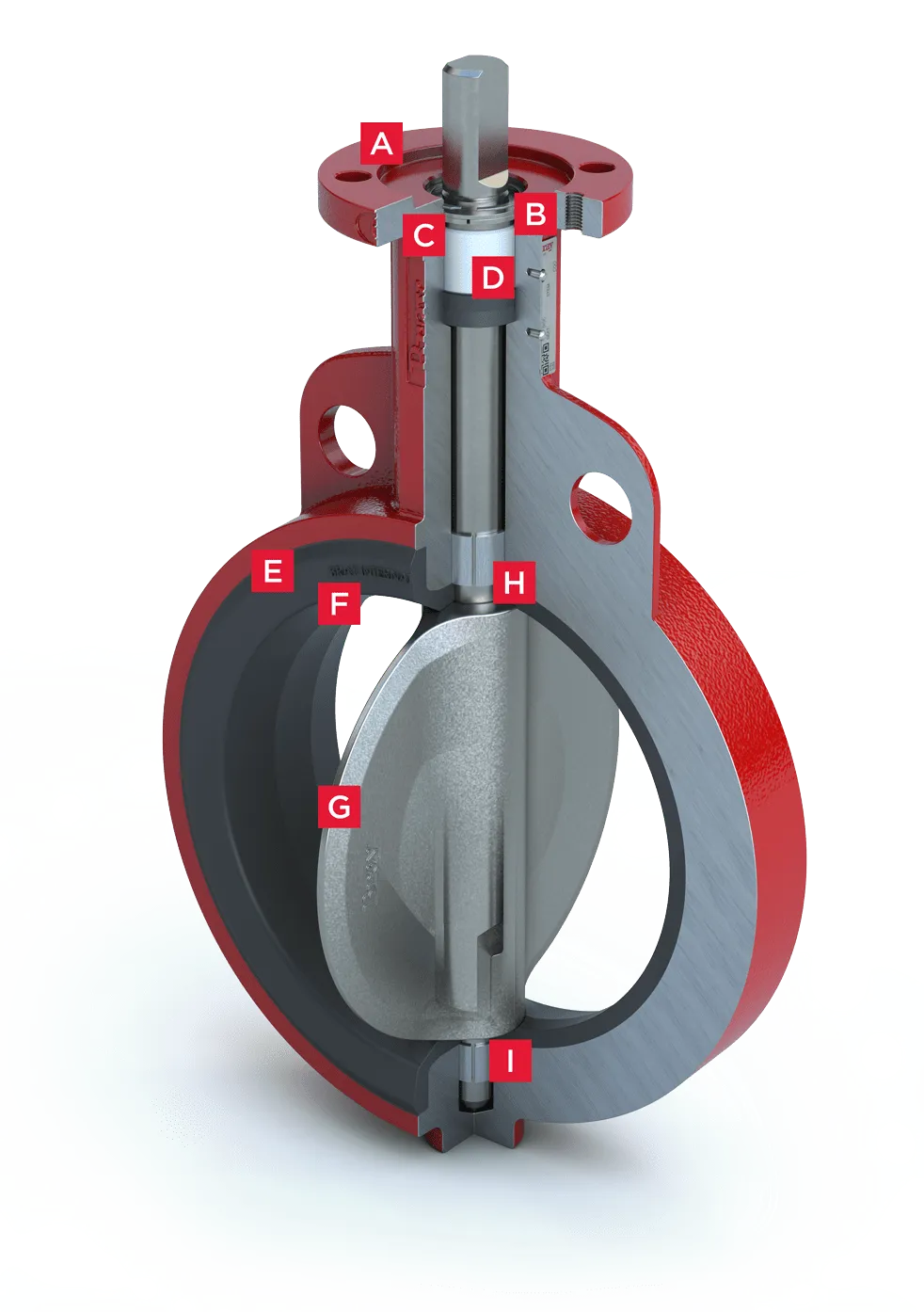
-
A. Digital Tag
Each valve is uniquely and easily identifiable by simply scanning the QR Code on the product identification tag in accordance to IEC 61406.
-
B. Electrostatic discharge through antistatic design
Electrostatic discharge through antistatic design (Ground washer and Top flange drilling).
-
C. Stem Design
The high-strength stem design combine blowout-proof functionality for safe operation and excpetional service life.
-
D. Stem Bushing
Non-corrosive, heavy duty acetal bushing absorbs actuator side thrust.
-
E. Robust Flange Sealing
Tear-dropped shaped seat face enables tight sealing with a wide variety of industrial flanges.
-
F. Molded-in Seat
Tightly controlled molding process produces accurate and repeatable dimensions, which leads to consistently lower torques over the valve’s lifetime.
-
G. Precision Profiled Disc Sealing Edge
Extends the valve life by reducing seat wear.
-
H. Upper and Lower Stem Bearings
Reduce operating torque and increase reliability in high cycle applications.
-
I. End of Line Capability
Lug style valve allows for sealing at full rated pressure even when the downstream flange is removed.
Explore More Bray Insights
Learn Even More About How Bray’s Solutions Can Impact Your Business